
How to Keep a Dust-Free Body Shop: Managing Sanding Debris
For body shops, a clean work environment is paramount. Sanding debris, however, can be a persistent enemy, harming not just the aesthetics of your shop but also the quality of your work and the health of your employees. This comprehensive guide from Fastplus Abrasives will equip you with the knowledge and tools to create a dust-free haven in your body shop.
Understanding Sanding Debris in the Body Shop
In any body shop environment, sanding debris constitutes a significant byproduct of the refinishing process. Understanding its composition, sources, and associated health hazards is crucial for maintaining a safe and productive workspace.
Sources of Sanding Debris

The sources of sanding debris in a body shop are diverse and encompass nearly every stage of the refinishing process:
- Body Filler Sanding: During the repair process, body fillers are often applied to repair dents and imperfections in vehicle surfaces. Sanding these fillers smooths the surface but generates fine dust particles.
- Primer and Paint Sanding: Sanding is a critical step in preparing surfaces for primer and paint application. Sanding removes imperfections, promotes adhesion, and creates a smooth surface for paint. However, this process also produces a significant amount of debris.
- Clear Coat Sanding: After applying the clear coat, sanding is often required to achieve a uniform finish and remove orange peel or other surface imperfections.
- Metal Surface Preparation: Sanding may also be necessary during the preparation of metal surfaces, such as removing rust or corrosion before applying protective coatings.
Health Hazards of Inhaling Sanding Debris
Inhaling sanding debris poses serious health risks to automotive technicians and other personnel working in body shop environments. Some of the primary health hazards associated with exposure to sanding debris include:
- Respiratory Issues: Fine particles released during sanding can be easily inhaled into the lungs, leading to respiratory problems such as coughing, wheezing, shortness of breath, and exacerbation of pre-existing conditions like asthma.
- Skin Irritation: Direct contact with airborne dust can cause skin irritation and dermatitis, particularly in individuals with sensitive skin.
- Eye Irritation: Sanding debris can irritate the eyes, leading to redness, itching, and discomfort. Prolonged exposure may even cause more severe eye injuries.
- Potential for Occupational Diseases: Chronic exposure to airborne contaminants in body shop environments may increase the risk of developing occupational diseases such as pneumoconiosis (e.g., silicosis from inhaling silica dust) or occupational asthma.
The Consequences of Dust Build-Up
Dust accumulation in a body shop environment can have far-reaching consequences that extend beyond health hazards. From equipment wear to quality control issues, understanding the implications of dust build-up is essential for maintaining a safe and efficient workspace.
Abrasive Wear on Tools and Machinery:
- Dust particles settle on tools and machinery, leading to abrasive wear and tear over time.
- Excessive dust accumulation can compromise the performance and longevity of equipment, necessitating frequent maintenance and replacement.
- Abrasive particles in the dust can exacerbate wear on moving parts, affecting precision and accuracy in machining processes.
Impact on Paint Finishes:
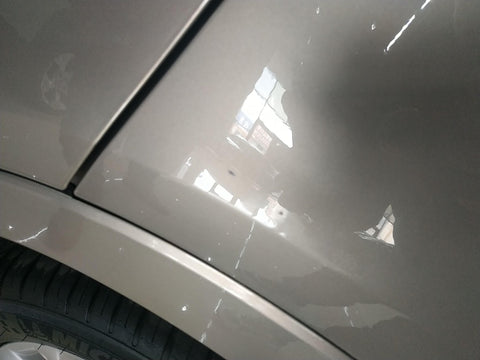
- Dust settling on freshly painted surfaces can mar the finish, resulting in imperfections such as bumps, pits, and rough texture.
- Contaminated paint surfaces may require extensive rework, including sanding and repainting, leading to increased labor costs and production delays.
- Quality control standards may be compromised, resulting in customer dissatisfaction and reputational damage for the body shop.
Fire Hazards in Ventilation Systems and Electrical Components:
- Dust accumulation in ventilation ducts and filters reduces airflow and ventilation efficiency, increasing the risk of overheating and fire hazards.
- Combustible dust particles in the air pose a significant fire hazard, particularly in areas where sparks or hot surfaces are present.
- Electrical components, such as motors and switches, can become clogged with dust, leading to overheating and potential ignition sources.
Diminished Efficiency and Productivity:
- Dust accumulation can disrupt workflow by causing equipment malfunctions, necessitating downtime for repairs and maintenance.
- Workers may spend valuable time cleaning and removing dust from work surfaces, tools, and machinery, detracting from productive tasks.
- Production schedules may be delayed or interrupted due to the need for additional surface preparation and quality control measures.
- Employee morale and motivation may suffer in an environment plagued by dust-related issues, further impacting overall shop efficiency.
Creating a Dust Management Plan
An effective dust management plan necessitates a comprehensive approach that addresses various aspects of dust generation and control. Here's a detailed breakdown of key strategies to incorporate into your plan:
1. Source Control: Choosing the Right Sanding Products
To effectively manage dust in your body shop, it's essential to start at the source by selecting the right sanding products. Here are some key strategies to consider:
Low-dust sanding abrasives:
Opt for abrasives specifically designed to generate minimal dust. Fastplus Abrasives offers a wide range of such products to suit your sanding needs, including:
- Dust-free Ceramic Mesh Discs: These discs feature a specialized mesh design engineered to optimize airflow while minimizing dust production. The innovative construction allows for efficient material removal with minimal airborne particulates, resulting in cleaner work surfaces and improved air quality.
- Multi-hole Ceramic Sanding Discs: Designed with multiple perforations for enhanced dust extraction, these discs excel at removing material while simultaneously capturing dust at the source. The strategic placement of the holes ensures efficient airflow, resulting in reduced clogging and superior dust containment during sanding operations.
- Wet/Dry Fine Finishing Foam Discs: Ideal for both wet and dry sanding applications, these foam discs deliver exceptional finish quality with minimal dust emission. The soft yet durable foam construction conforms to contours and irregular surfaces, facilitating smooth and consistent sanding results while minimizing airborne dust.
- Film Sanding Discs: Constructed from high-quality film material, these discs offer exceptional durability and resistance to clogging, resulting in minimal dust generation during sanding. The smooth surface of the film provides consistent abrasive performance, ensuring precise material removal without the risk of dust contamination.
Vacuum-attached sanding tools:
Consider using sanding blocks or hand sanders equipped with dust collection ports that connect directly to a vacuum cleaner. These tools capture dust particles at the source, significantly reducing airborne dust and improving overall air quality in the workspace.
2. Dust Collection: Investing in the Right Equipment
A powerful vacuum cleaner is vital for effective dust control. Here's what to consider:
- HEPA filtration: Look for a High-Efficiency Particulate Air (HEPA) filtered vacuum cleaner. HEPA filters capture particles as small as 0.3 microns, ensuring even the finest sanding dust gets trapped.
- Automatic filter cleaning: Automatic filter cleaning systems prevent clogging and maintain optimal suction power.
- Hose length and reach: Choose a vacuum with a hose long enough to reach all work areas comfortably.
3. Shop Practices: Habits for a Dust-Free Environment
- Designated sanding areas: Confine sanding activities to specific, well-ventilated areas within the shop.
- Containment techniques: Utilize drop cloths or plastic sheeting to contain dust during sanding projects on vehicles.
- Cleaning procedures: Establish regular cleaning routines. Vacuum floors and surfaces frequently, paying close attention to corners and hard-to-reach areas. Avoid sweeping which can stir up dust. Damp cloths or mops are preferable for final cleaning after vacuuming.
- Personal protective equipment (PPE): Always ensure employees wear appropriate dust masks or respirators rated for silica dust to safeguard their health.
Conclusion: A Clean Shop is a Successful Shop
By prioritizing dust control, you're not just creating a cleaner work environment; you're safeguarding your employees' health, ensuring the quality of your work, and boosting your shop's efficiency. With the right strategies, tools, and a commitment to best practices, you can achieve a dust-free haven in your body shop.
Buy Factory-Direct Fastplus Abrasives
Want to purchase high-quality, factory-direct sanding discs, sanding sheet rolls, and film abrasive discs for automotive applications? Try Fastplus Abrasives today and place your orders online!